
Pharmaceutical Packaging Solutions
Medications are lifelines. Their packaging should be too. Oxipack's leak detection ensures secure seals, protects patient health, and simplifies regulations.
Secure Pharma Quality: Precision Leak Detection for Pharmaceutical Packaging
Unlike food, where a leak might mean a soggy snack, in pharmaceuticals, a single breach can have devastating consequences. That's why Oxipack's advanced leak detection systems are built with the utmost precision. Our technology ensures your packaging meets the strictest standards, guaranteeing the sterility and efficacy of every life-saving dose.
Pharmaceutical Packaging Leak Testing Methods
Oxipack utilizes cutting-edge non-destructive testing methods, like vacuum decay, to guarantee the integrity of pharmaceutical packaging without harming the product. These methods excel at detecting even the most minuscule leaks, ensuring the safety, freshness, and extended shelf life that your product deserves.
Frequently Asked Questions
Oxipack specializes in providing vacuum decay leak testers, employing a non-destructive method for detecting leaks in packaging. Vacuum decay involves measuring the change in pressure within a sealed chamber over time, which serves as an indicator of any leaks present in the packaging. Our range of leak detection machines utilizes this advanced technique, offering clean, dry, and highly precise leak tests without the need for traditional methods such as a bubble test or a trace gas.
Container closure integrity testing, also known as pharmaceutical package testing, is a crucial aspect of ensuring the quality and safety of pharmaceutical packaging. It involves using quality inspection tools to assess the integrity of sealed containers. One common method is vacuum decay testing, where the sealed container is subjected to a vacuum to detect any leaks or breaches in its integrity. This process helps pharmaceutical companies maintain the quality and efficacy of their products by ensuring that they are properly sealed and protected.
Leak detection methods such as vacuum decay and bubble tests are widely utilized in pharmaceutical packaging. By conducting thorough leak tests, manufacturers can ensure container closure integrity testing, thereby safeguarding product safety. These techniques, facilitated by leak detectors, play a crucial role in maintaining the required quality standards and preventing potential product contamination or loss.
Maintaining the integrity of sealed packages is critical to uphold quality standards and prevent product loss. One effective solution utilized across industries is vacuum decay testing. This method, facilitated by specialized leak detection machines, provides accurate and reliable results. By subjecting sealed packages to a vacuum environment, we can precisely detect any leaks through monitoring pressure changes. Our comprehensive leak test procedure ensures that even the smallest leaks in package seals are identified. With our expertise and state-of-the-art leak test equipment, including vacuum chambers and pressure sensors, we offer a seamless integration of leakage testing into your production process. This ensures that your products remain secure and intact, meeting stringent quality requirements. Whether you're in pharmaceuticals, food packaging, or any other industry requiring meticulous quality control, our vacuum decay testing solutions provide the assurance you need to safeguard your products to an acceptable quality level.
The pharmaceutical packaging industry relies on various methods such as leak detection, including vacuum decay and bubble tests, to conduct container closure integrity testing. These techniques, facilitated by specialized leak detectors, help maintain an acceptable quality level by swiftly identifying any leaks or flaws in the packaging seals through leak checks and leakage tests.
Unlike traditional methods that may use bubble tests, or traceable gases, Oxipack's exclusive testing system detects the smallest pressure differences without damaging the packaging. This approach is clean, dry, and highly precise. Oxipack's non-destructive leak detection method is based on vacuum decay ASTM F2338 standard. You can read more here.
Investing in Non-Destructive Leak Testing
Choosing Oxipack's non-destructive leak testing solutions not only ensures the highest quality and safety standards for your products but also offers a significant return on investment by reducing material waste and preventing contamination.
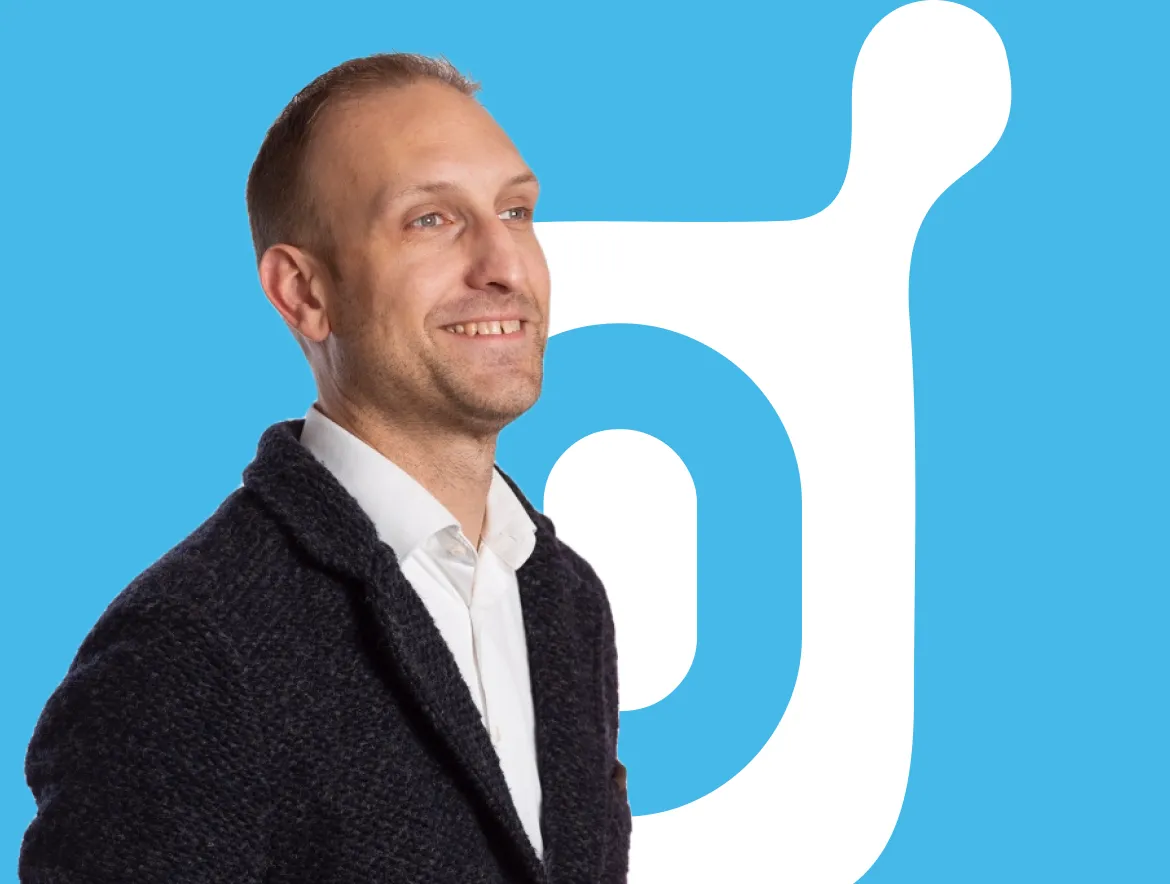