.webp)
Testing Vacuum Packaging For Leaks
At Oxipack, we understand the critical importance of maintaining the integrity of vacuum packaging. Our state-of-the-art non-destructive leak detection solutions are designed to ensure your vacuum-packed products are perfectly sealed, every time.
why Vacuum packaging?
Vacuum packaging is essential for preserving the freshness and extending the shelf life of perishable goods by removing air and minimizing exposure to environmental factors. Our leak testing ensures the vacuum seal is intact and effective, providing maximum protection and maintaining the quality of the contents throughout their transport and storage.
Our technology detects the smallest leaks, down to micron levels, critical for maintaining the vacuum seal's effectiveness. This high sensitivity ensures that even the slightest imperfections are identified, safeguarding product quality and shelf life.
Designed for efficiency, our vacuum packaging testers achieve significant pressure differences quickly—typically within seconds. This rapid testing capability allows for high throughput, ensuring that production lines maintain peak efficiency without sacrificing precision.
Designed with the end-user in mind, our vacuum packaging leak detection machines are a breeze to use and integrate seamlessly into your existing production line. They work fast, giving you results that are immediate and actionable. It means less downtime, more productivity, and packaging integrity you can count on.
In line with our commitment to a zero-waste world, our leak detection methods are an essential part of sustainable packaging processes. By ensuring leak-free packaging, we help you reduce waste, save resources, and contribute positively to environmental conservation.
By utilizing non-destructive testing methods, our systems ensure that products remain completely intact and market-ready after testing, minimizing waste and enhancing sustainability.
Built to operate reliably in demanding industrial environments, our leak testers feature a robust construction that withstands continuous use, making them an enduring part of quality control processes.
Oxipack's leak detection systems are specifically engineered for vacuum packaging, ensuring optimal preservation and integrity of products sealed under vacuum conditions. These systems are crucial for industries where product freshness and seal integrity are paramount.
The Importance of Non-Destructive Leak detection for Vacuum Packaging
Non-destructive leak testing keeps vacuum seals intact, maximizing product freshness and extending shelf life. This method ensures early leak detection, preventing contamination and building consumer confidence in product quality.
Frequently Asked Questions
Detecting leaks in vacuum packaging is crucial because even the smallest leaks can significantly affect the quality of the packaged product. These micro leaks can occur during the manufacturing process of the packaging and are often difficult to detect. If vacuum packaging is not leak-tight, oxygen can enter the package, compromising the quality, freshness, and safety of the product. This can result in spoilage, discoloration, off-flavors, and the growth of harmful bacteria that require oxygen to survive. By promptly detecting and addressing leaks, manufacturers can ensure that their vacuum packaging effectively preserves the quality and safety of the packaged products. Moreover, early detection of leaks can help minimize waste, reduce the risk of recalls, and save costs associated with potential product spoilage or safety issues.
Non-destructive leak testing of your vacuum packaging has several advantages, for example it ensures better product safety, higher product quality, lower environmental impact, and it will save you costs. Are you curious about how much costs it will save you? Download our free white paper or contact us via sales@oxipack.com.
We have different methods of testing vacuum packaging. A pack of vacuum sausages requires a completely different method than, for example, vacuumed coffee. Contact our specialists at sales@oxipack.com for tailored advice.
The leaks our leak testers find are so small they would only become noticeable after hours, resulting in loose packaging. An example of saving storage time can be read in our case on vacuum coffee packaging. Contact us through sales@oxipack.com to learn how you can optimize your testing to avoid production of leak packaging.
This depends entirely on the type of product and packaging. Often leaks which only become visible after hours or days can easily be discovered immediately after production.
Since the leak tester is non-destructive, the packaging can be returned to the production line.
Our Packaging Methods
Explore our other packaging methods.
Insights
Explore our latest News, Blogs, Cases and Whitepapers
Ready to Enhance Your Vacuum Packaging Process?
Contact us today to learn more about how Oxipack can revolutionize your packaging quality control. Let’s seal the deal on excellence together.
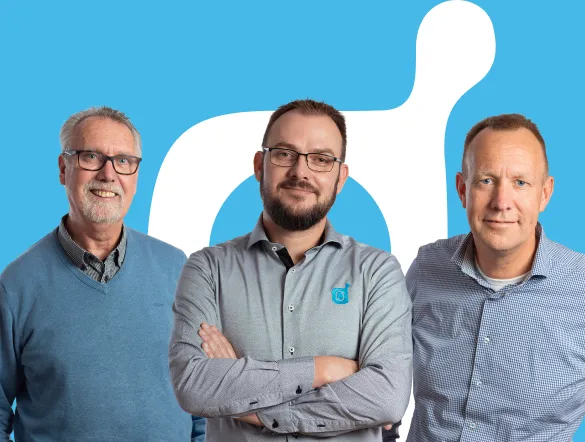