Ever wondered how companies ensure that the products you buy are perfectly sealed and safe? Automated leak detection is the innovative solution that guarantees the quality and safety of these products, ensuring they reach consumers without any issues.
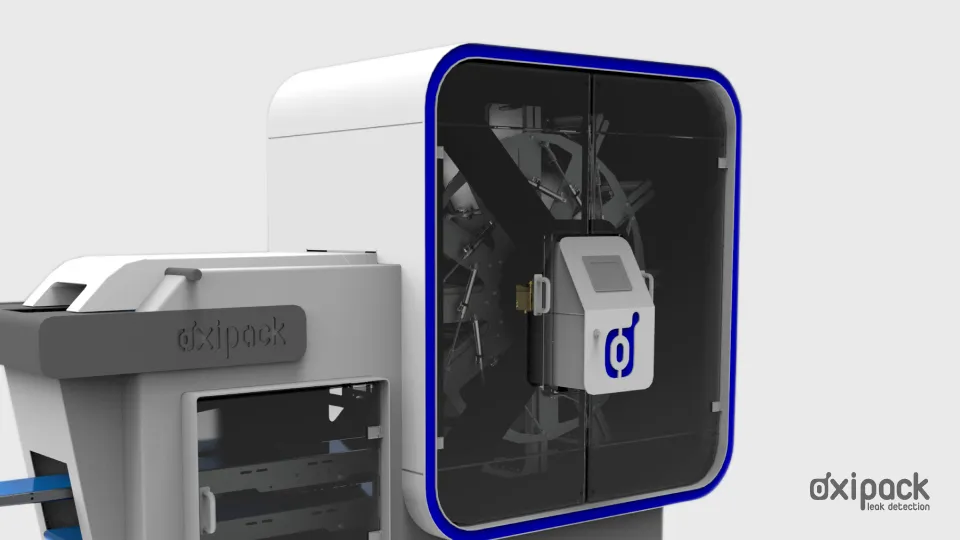
Benefits of Automated Leak Detection
1. Enhanced Quality Control
Automated leak detection systems meticulously test the quality of every package, ensuring each one meets strict standards. This process eliminates the variability of manual inspections and provides consistent, reliable results.
2. Efficiency in Production
With in-line leak detectors integrated into the production line, the need for additional manual labor is significantly reduced. This not only speeds up the process but also reduces labor costs.
3. Non-Destructive Testing
Our automated leak detectors utilize non-destructive methods, such as the vacuum decay method. This means packages that pass the test can continue through production without being damaged, reducing waste and saving costs.
4. Real-Time Feedback
Automated systems provide immediate feedback on the production process, allowing for quick adjustments and ensuring continuous quality control. This instant data analysis helps in identifying potential issues before they escalate.
5. Waste Reduction
Early detection of leaks prevents defective packages from reaching the market, reducing product waste. This not only saves costs but also supports sustainable manufacturing practices.
6. Cost Savings
By integrating leak detection into the production process, companies can avoid costly recalls and rework later on. Automated systems ensure products are leak-free from the start, minimizing additional costs down the line.
Automated Leak Testing Machines by Oxipack
The Rotary
The Rotary is designed to test flexible MAP-packaging using the vacuum decay method. Capable of testing up to 120 packages per minute, this machine is fully integrated into the production line. It provides instant feedback on package integrity, with defective packages automatically sorted and separated from the production flow.
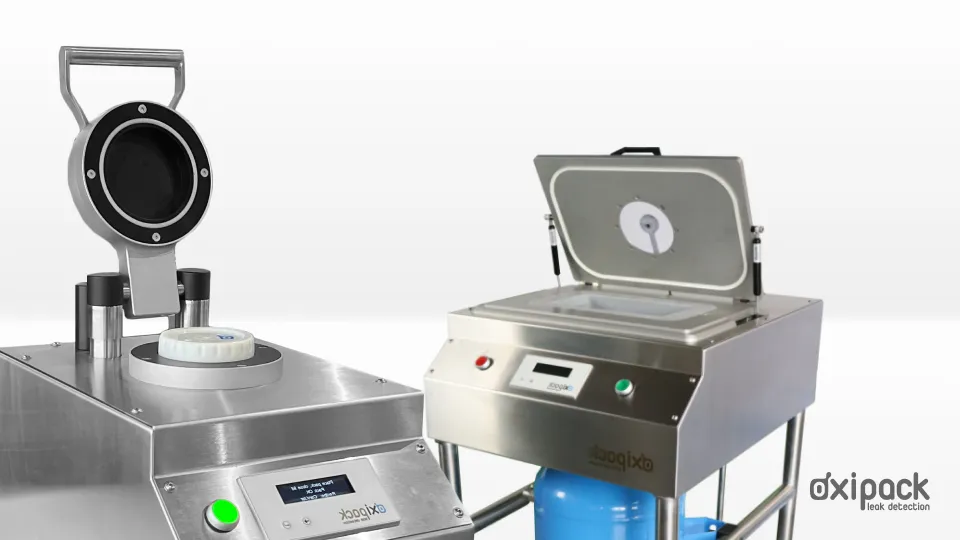
Vacuum Leak Tester In-line
Ideal for vacuum-packed products like coffee and yeast, the Vacuum Leak Tester In-line performs automated sample testing. It selects packages from the conveyor belt and tests each one for leaks, providing complete control over the production process and significantly reducing the occurrence of leaks.
Automated leak detection is a game-changer for industries that require high standards of packaging integrity. By integrating these advanced systems into your production line, you ensure that your products meet the highest quality standards while reducing waste and saving costs. Curious about how Oxipack can help you implement an automated leak detection solution? Contact us to find the perfect fit for your packaging needs.