Embracing Automation: The Future of Quality Control in the Packaging Industry
The Importance of Quality Control in Packaging
The packaging industry is pivotal in protecting and preserving products during transportation and storage. To ensure that products reach customers in excellent condition, the industry must adhere to strict quality control processes. Recently, a transformative shift has occurred with the adoption of automation to enhance quality control and meet growing consumer demands. This shift has introduced various methods for assessing package quality, including destructive and non-destructive, manual and automated techniques. Here, we explore the significant advantages of non-destructive automated quality control systems.
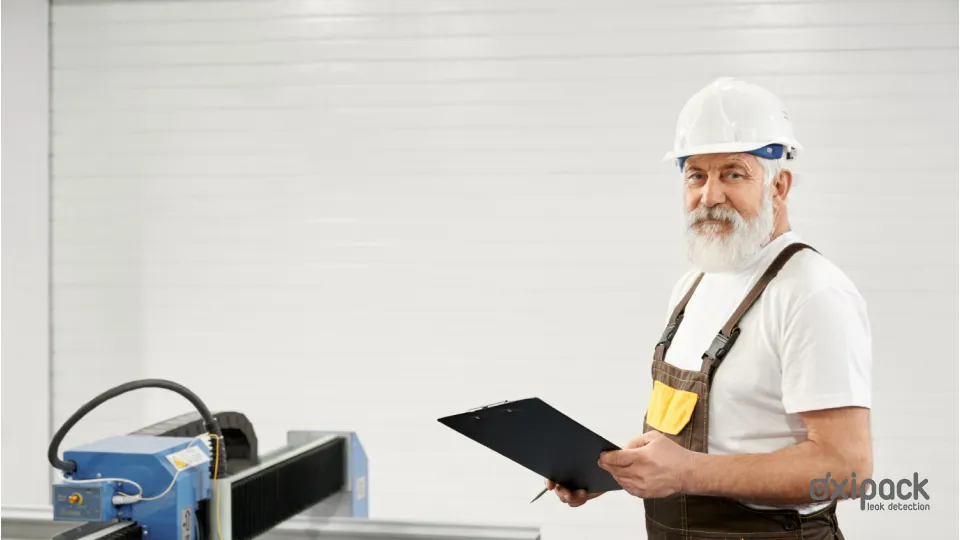
The Advantages of Automated Quality Control
1. Consistency:
Automated quality control systems deliver a remarkable level of consistency and precision, eliminating the variability seen in manual inspections due to human performance differences. This ensures a uniform standard of quality across all products.
2. Comprehensive Testing:
Unlike random sampling, automated quality control machines meticulously examine the entire production line, ensuring every package is scrutinized. This thorough approach significantly reduces risks by guaranteeing all moving packages are tested and leak-free.
3. Data Analysis:
Automated quality management systems can collect and analyze large volumes of data in real-time. This capability provides insights into production processes, helping identify potential quality issues before they become major problems.
4. Faster Intervention:
Leveraging data analysis, automated systems enable swift interventions in case of anomalies. This results in reduced production downtime, saving 30-60 minutes that would otherwise be lost in process reconfiguration or repackaging.
5. Economical Labor Utilization:
Automated quality inspection and leak testing streamline labor requirements compared to standalone machines. This efficiency not only reduces labor costs but also enhances overall operational efficiency.
6. Scalability:
The scalability of automated quality control systems makes them exceptionally suitable for dynamic production environments with fluctuating demands. This adaptability is ideal for high-volume manufacturing settings.
Implementing Automated Quality Management Systems
Integrating automated quality management systems can revolutionize production processes. Non-destructive quality control techniques help reduce waste and increase customer satisfaction, contributing to sustained success and profitability.
In-Line Quality Control Machines
At Oxipack, we specialize in developing non-destructive manual quality control machines (stand-alone) and tailor-made automated quality control machines (in-line). The key distinction between these approaches lies in labor requirements: stand-alone testers require manual labor, while in-line leak testing is fully automated.
Automated quality control systems represent a significant investment but offer numerous advantages. Wondering what we recommend for your production line? Feel free to contact us for more information and tailored solutions.