Is your packaging silently failing you? Tiny leaks might seem insignificant, but they can wreak havoc on your product's quality and safety. Here's where air leak testing comes in – a crucial quality control measure that safeguards your brand reputation.
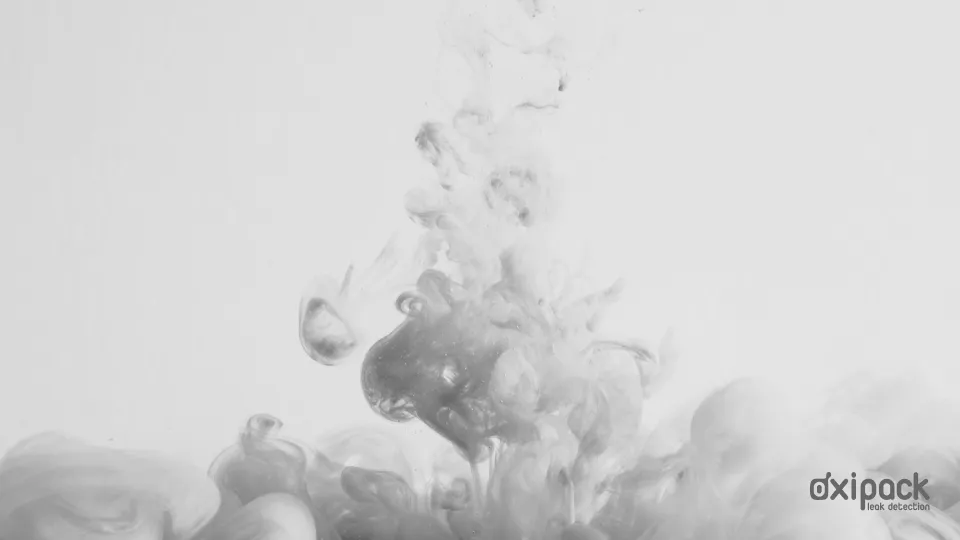
Air Leak Testing: Protecting Your Products from the Inside Out
Packaging acts as a shield, protecting your products from external threats like contamination and environmental factors. But what about unseen breaches? Air leak testing is your secret weapon, identifying even the most minuscule leaks that could compromise your product's integrity.
This essential quality control procedure involves subjecting packaging to controlled pressure changes. Any fluctuations signal a potential leak, ensuring your product remains safe and effective. It's a cornerstone practice in various industries, including food, pharmaceuticals, cosmetics, and more. Here's how air leak testing safeguards your products:
- Preserves Product Quality: Leaks can allow oxygen , moisture, or other contaminants to enter the packaging, potentially spoiling or degrading your product. Air leak testing ensures a secure environment for your product, maintaining its intended quality.
- Enhances Safety: Leaks can compromise the effectiveness of certain products, particularly pharmaceuticals. Air leak testing guarantees that your packaging functions as intended, protecting consumers from potential harm.
- Extends Shelf Life: Leaks can shorten a product's shelf life. Air leak testing helps ensure your products stay fresh and effective for their intended duration.
Air Leak Detection Methods: Choosing the Right Fit
Several air leak detection methods exist, each with their strengths and limitations.
Here's a breakdown of some common methods:
- Pressure Decay Method: This method pressurizes the package and monitors pressure drops over time. While effective for larger leaks, it might miss smaller ones.
- Bubble Emission Test: The package is submerged in liquid while a pressure difference is introduced. Leaks are identified by observing bubbles. However, this method damages the packaging and renders it unusable.
- Dye Penetration Test: During the test, a package is filled with a colored dye solution, typically blue in color. If any leaks or openings are present in the package, the dye will seep out, indicating a potential breach in the package integrity.
- Microbial Ingress Test: Microorganisms are introduced into the package, followed by incubation. Microbial growth signifies a leak. This complex method requires a controlled environment and significant time.
- Trace Gas Leak Testing: Highly sensitive, this method uses gas as a tracer to detect leaks. However, it requires specialized equipment, making it expensive.
- Vacuum Decay Method: This method, employed by our air leak detection equipment, involves placing the package in a chamber and creating a vacuum. Pressure changes within the package indicate leaks. It's a highly sensitive, versatile, and cost-effective method suitable for various packaging types.
Choosing the Ideal Air Leak Detection Equipment
The best air leak detection method depends on several factors, including:
- Packaging Type: Different packaging materials require compatible testing methods.
- Sensitivity Needs: How critical is it to detect even the tiniest leaks?
- Leak Size: Are you primarily concerned with large or small leaks?
- Industry Regulations: Certain industries have specific testing requirements.
The vacuum decay method offers numerous advantages:
- Wide Applicability: Works with a broad range of packaging materials.
- Approved Technique: Meets industry regulations in food, pharmaceutical, and cosmetic sectors.
- High Sensitivity: Detects even the smallest leaks.
- Fast and Efficient: Offers rapid testing times.
- Cost-Effective: Provides a reliable solution without breaking the bank.
- Environmentally Friendly: Doesn't require harmful chemicals or gases.
For a detailed explanation of the vacuum decay test, its benefits, and a cost analysis highlighting potential savings, download our free whitepaper (insert link here)
The Right Choice for Impeccable Packaging
Selecting the appropriate air leak testing equipment requires careful consideration of each method's pros and cons. Choosing the right method ensures optimal product protection and cost-efficiency for your business.
Contact us today to discuss your air leak testing needs and discover how we can help you implement the most effective solution for your products.