Do you know what one tiny leak, invisible to the human eye, could do to your life-saving medication? This alarming possibility highlights the crucial need for evolving from outdated leak testing methods in the pharmaceutical industry. While the blue dye test has served its purpose, it's time to explore more reliable solutions that ensure the safety and efficacy of medication that countless lives depend on every year.
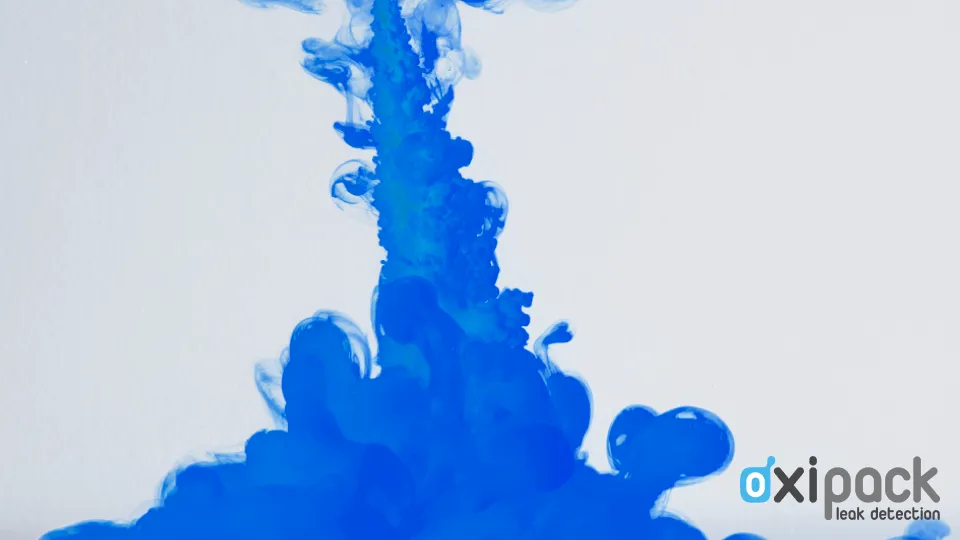
The Critical Role of Blue Dye Leak Testing
When it comes to pharmaceuticals, food, and cosmetics, maintaining the integrity of packaging isn't about quality alone; it's crucial for safety. Traditionally, the blue dye leak test has held a prominent role due to its simplicity and direct approach. This method involves applying a blue dye solution to packaging materials and then visually inspecting for signs of leakage.
Understanding Blue Dye Leak Testing
The blue dye leak test offers a straightforward approach to evaluating package integrity. This method utilizes a colored dye solution that mimics the consistency of potential contents. It primarily focuses on leak-prone areas like seals and joints. After application and a designated incubation period, the packaging is examined for signs of dye penetration, indicating a leak.
Scope and Limitations
The ASTM F1929 standard, specifically designed for spongelike medical packaging (e.g., pouches), employs the dye penetration method to assess seal integrity. This method is particularly relevant for penetrable materials commonly used in medical device packaging.
However, despite its widespread use, the blue dye leak test has limitations:
- Destructive: This method renders the product unusable, potentially leading to waste.
- Qualitative Results: It provides less precise, qualitative results rather than quantitative measurements.
- Lower Sensitivity: Compared to other methods, it has a lower sensitivity for detecting leaks.
- Subjectivity: Interpretation of results can be subjective, varying between operators.
- Limited Detection: It may miss certain types of leaks, particularly those with low permeability or in complex structures.
- Time-Consuming: The test process can be lengthy, impacting efficiency.
- Environmental Sensitivities: Results can be influenced by environmental factors like temperature and humidity.
A Modern Alternative: The Vacuum Decay Method
The vacuum decay method offers a compelling and non-destructive alternative. This approach provides specific and precise results, surpassing the blue dye test in both sensitivity and objectivity. Additionally, it is faster, more consistent, and more reliable, minimizing subjectivity and variability.
Embracing a New Era of Packaging Integrity Testing
Remember that tiny, invisible leak we mentioned at the beginning? The one that could potentially compromise your life-saving medication? By embracing modern alternatives like the vacuum decay method, we can collectively move towards a future where such scenarios become a distant memory.
The blue dye test, while instrumental in the past, no longer meets the evolving needs of the pharmaceutical industry. Just as technology and medicine have advanced, so too should our methods for ensuring the safety and efficacy of the products we rely on. By transitioning to a more sophisticated and reliable approach, we safeguard not only the integrity of individual packages but also the well-being of countless individuals who depend on these medications every day.
Interested in a more effective solution? Download our whitepaper on the cost-saving benefits of the vacuum decay method and contact us to discuss how we can assist in your transition.