Imagine you're a surgeon, but your only tool is a blunt knife. That's the reality of bubble leak testing in today's day and age. It's time to sharpen our approach with non-destructive leak detection methods, like those developed by Oxipack, that not only excel in precision but also in data management.
Our approaches to ensuring quality and safety in packaging and product integrity must continually evolve. Traditional bubble leak testing, a method once considered the gold standard, is now showing its limitations, much like a surgeon operating with outdated tools. As we navigate through the intricacies of packaging integrity, especially in sectors like pharmaceuticals and food production, the shift towards non-destructive leak detection becomes not just preferable, but essential.
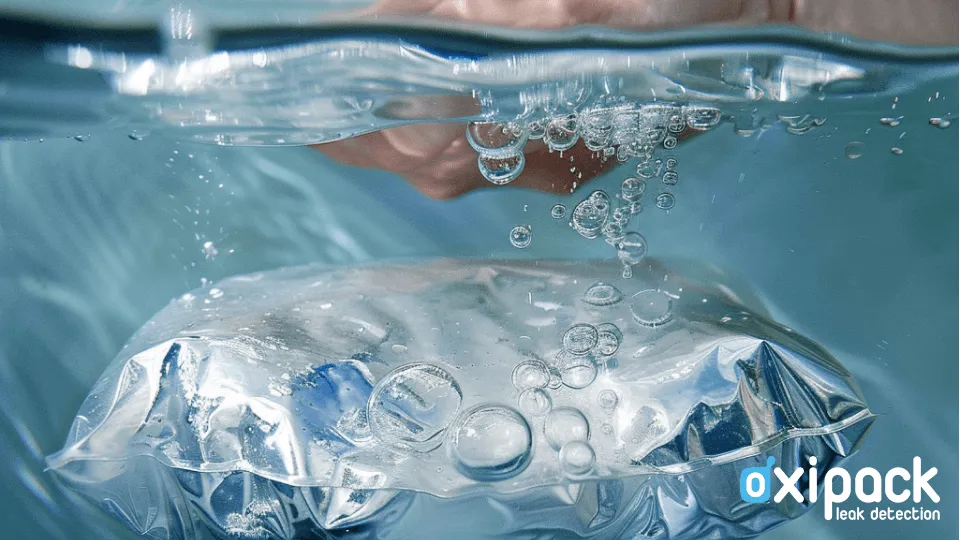
The Bubbles Burst: Understanding the Shortcomings
Bubble leak testing, for all its simplicity, has significant drawbacks. The process involves submerging the package in water and observing for bubbles, indicating a leak. However, detecting minute leaks is nearly impossible, and the method is highly subjective, relying on the operator's interpretation. The risk of human error is high, and the inability to quantify the leak size is a major limitation.
Moreover, bubble testing is fundamentally destructive. The product, once tested, cannot return to the supply chain, leading to increased waste and costs. This is counterintuitive in an era where sustainability and cost-efficiency are vital.
The Era of Precision: Non-Destructive Leak Detection
Enter non-destructive leak detection, a game-changer in the domain of quality control. Companies like Oxipack are at the forefront of this revolution, offering sophisticated solutions like vacuum decay methods, which are clean, dry, and exceptionally precise. This technique, as opposed to bubble testing, is non-invasive and leaves the package and product intact.
The advantages are multifold:
- Precision and Sensitivity: Non-destructive methods can detect the smallest pressure differences, identifying leaks that would otherwise go unnoticed in bubble testing.
- Quantifiable Results: Unlike bubble testing, which is subjective and lacks control over quality data, Oxipack’s advanced solutions capture and store detailed test results, providing an invaluable dataset for your quality system. This objective data enhances traceability, process optimization, and regulatory compliance, making it an integral part of modern quality control systems.
- Cost-Effectiveness and Sustainability: By preserving the integrity of the product, these methods reduce waste, aligning with sustainability goals while also being economically advantageous.
- Versatility: Non-destructive techniques can be adapted for a wide range of packaging types and sizes, a stark contrast to the one-size-fits-all approach of bubble testing.
Redefining Industry Standards
As the industry searches for new materials to reduce plastic usage, thorough quality control becomes increasingly a must. Not all materials are suitable for testing by traditional methods, especially with the rising use of paper-based materials that cannot withstand the rigors of bubble testing. This shift towards innovative packaging solutions necessitates advanced leak detection methods that can accommodate a broader range of materials without compromising the integrity of the package or the product within.
The transition from traditional to innovative testing methods is more than just a technological upgrade; it's a paradigm shift in how we perceive quality control. It's about moving from a reactive to a proactive approach. Non-destructive leak detection not only identifies flaws but also contributes to process improvements, reducing the likelihood of future defects.
Embracing the Future
The disadvantages of bubble leak testing highlight a broader issue in many industrial practices - reliance on outdated methods in a world where precision is key. Non-destructive leak detection is not just an alternative; it is the future, steering industries towards a more efficient, sustainable, and accurate era. It's time to leave the blunt tools behind and embrace the sharp precision of modern technology. Let's not just find leaks; let's prevent them.