Why Non-Destructive Leak Detection is the Perfect Solution for Your Packaging Needs
Maintaining the quality and efficiency of your packaging is essential in today's competitive market. Non-destructive leak detection provides an ideal solution by preserving product integrity, reducing waste, and minimizing costs. But what makes this method stand out?
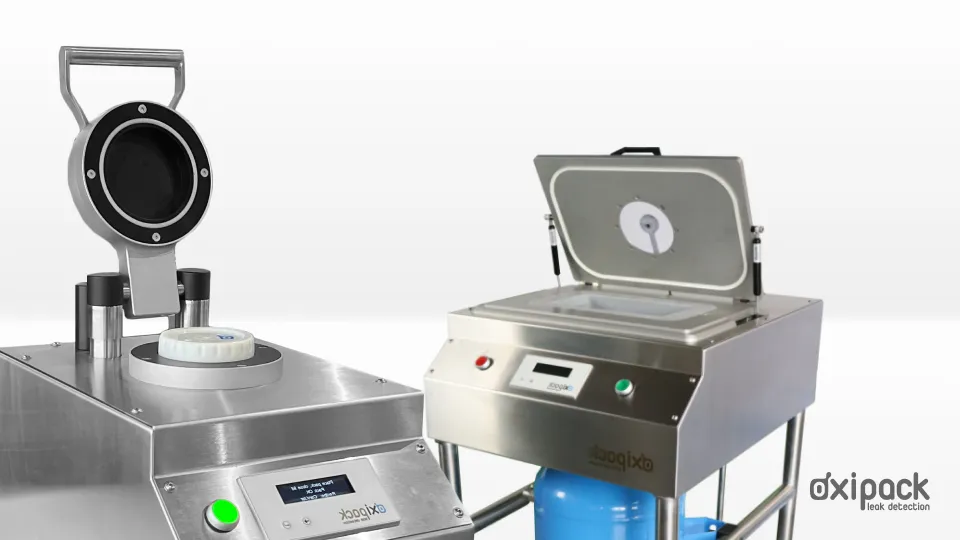
The Importance of Leak Detection in Various Industries
Leak detection is essential in the food and beverage, pharmaceutical, and cosmetic industries for several reasons:
- Product Integrity and Quality: Ensuring that packaging is leak-free preserves the quality of the product inside.
- Regulatory Compliance: Meeting industry standards and regulations for packaging integrity.
- Cost Savings: Reducing waste and avoiding the costs associated with defective packaging.
- Extended Shelf Life: Leak-free packaging helps in maintaining the product's freshness and longevity.
- Brand Reputation: Reliable packaging enhances customer trust and brand reputation.
- Customer Satisfaction: Delivering products in perfect condition ensures customer satisfaction.
The Cost Benefits of Non-Destructive Leak Testing
While the initial investment in non-destructive leak test equipment might seem significant, many companies recoup this cost within a year. Traditional destructive leak testing renders the packaging unusable after testing, leading to significant waste. In contrast, non-destructive leak testing allows approved packaging to be returned to the production line, saving costs and eliminating unnecessary waste. You can determine how long it will take to recoup your investment in our white paper.
Common Leak Testing Methods
Different packaging types and products require various leak testing methods. Here are some common methods:
- Visual Inspection: A simple, destructive method where packaging is visually examined for leaks.
- Immersion Test: A destructive method where packaging is immersed in water, and air bubbles indicate leaks.
- Helium Leak Test: Often a destructive method where helium is injected into the packaging, and a detector checks for escaping helium.
- Pressure Test: A non-destructive method where packaging is pressurized, and pressure loss indicates leaks.
- Vacuum Detection: A non-destructive method used by Oxipack, where packaging is placed in a vacuum environment, and changes in vacuum levels indicate leaks.
Oxipack Leak Detection Equipment
At Oxipack, we primarily use the vacuum decay method, an ASTM F2338 Standard Test Method, for non-destructive leak detection. This method is suitable for both flexible and rigid packaging, including pouches, bags, cups, pods, bottles, and cans. We have developed equipment for nearly every type of packaging, and we are eager to assist you in finding the right solution.
How Our Leak Test Equipment Works
Our leak detection equipment is designed to be easy to operate:
- Placement: Place the packaging into the machine.
- Testing: The machine creates a pressure difference and reads it on the display.
- Results: At the end of the test, the machine indicates if the packaging is leak-tight (green light) or leaking (red light). Leak-tight packaging can be returned to the production line undamaged.
For those who prefer automated operations, we offer in-line solutions tailored to your needs. For example, our in-line Rotator can test up to 120 flexible MAP pouches per minute, providing automated and efficient leak detection.
Our Leak Testing Machines
Over the years, we have developed various leak testing machines for flexible, rigid, and vacuum packaging. Here are some of our standard machines:
Flexible Packaging
- Stationary Leak Tester or Pouch Leak Tester
- Stationary Leak Tester XXXL (for up to 25 kg bags)
Rigid Packaging
- Multi Leak Tester (for pods and jars)
- Stationary Leak Tester XS/M
- Can Leak Tester
- Bottle Leak Tester
- Container Closure Integrity Tester
Vacuum Packaging
- Vacuum Leak Tester
- Vacuum-Sealed Leak Tester
- Vacuum Pressure Tester
Non-destructive leak detection is the ideal solution for ensuring packaging integrity while reducing waste and costs. If you would like more information about our leak detection solutions, please feel free to contact us.