Ensuring the reliability of pharmaceutical packaging is not just a regulatory requirement but a critical aspect of patient safety and product efficacy. Imagine the consequences of a contaminated medication due to a compromised packaging seal. This is where the guidelines of USP 1207 come into play, offering a robust framework for Container Closure Integrity Testing (CCIT). This blog post delves into the significance of USP 1207 and how it shapes the landscape of pharmaceutical packaging.
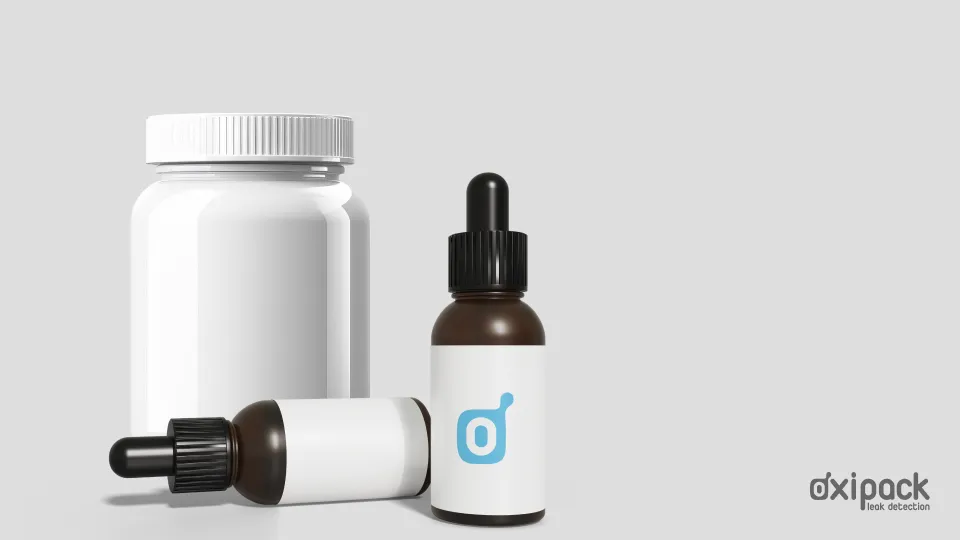
The Importance of CCIT Outlined in USP 1207
Maintaining Product Quality and Safety
USP 1207 encompasses a wide array of container closure systems, including vials, ampoules, bottles, and medical devices. The guidelines emphasize the necessity of container closure integrity to prevent contamination by microorganisms, moisture, and other harmful substances, thereby preserving the drug's quality and patient safety. Effective CCIT ensures that external factors such as light and oxidation do not degrade the product.
USP Chapter 1207: Container Closure Integrity Testing
Key Principles and Requirements
USP chapter 1207 sets forth principles and requirements for container closure integrity testing, including:
- Identification of Leaks: Methods like vacuum decay, microbial ingress, and dye ingress are designed to detect potential leaks in packaging. These methods identify contamination entry points, ensuring product safety.
- Quality Control: CCIT is a critical quality control measure in pharmaceutical manufacturing. By assessing the integrity of container closure systems, manufacturers can ensure compliance with USP 1207 standards, maintaining product quality, potency, stability, and efficacy.
- Regulatory Compliance: CCIT is essential for meeting regulatory requirements from agencies such as the FDA and EMA. Adherence to USP 1207 guidelines demonstrates compliance, supporting product safety and efficacy.
CCIT Methods in USP 1207
Non-Destructive Testing with Vacuum Decay
Among the methods outlined in USP 1207, the vacuum decay method stands out for its sensitivity and non-destructive nature. At Oxipack, we utilize this method to ensure packaging integrity. The process involves applying a vacuum to the sealed container and monitoring pressure changes over time to detect potential leaks.
Advantages of the Vacuum Decay Method
Sensitivity and Precision
The vacuum decay method is highly sensitive, capable of detecting small leaks at a sub-micron level. This sensitivity is crucial for ensuring the integrity of pharmaceutical packaging.
Non-Destructive Testing
Unlike destructive methods, vacuum decay testing does not damage the container or its contents, allowing for larger sample sizes and preserving the integrity of remaining products.
Rapid and Versatile Testing
The method provides fast results, making it efficient for production processes. It is versatile, applicable to various container types and both liquid and lyophilized products.
USP 1207 Acceptance Criteria
Ensuring Compliance and Product Quality
USP 1207 outlines acceptance criteria to evaluate the integrity of container closure systems. These criteria vary based on container types, materials, and sealing mechanisms. Compliance with these standards is crucial for maintaining product safety, efficacy, and regulatory approval.
Oxipack’s Alignment with USP 1207
Commitment to Quality and Compliance
Oxipack's vacuum decay method aligns with USP 1207 acceptance criteria, offering a reliable solution for container closure integrity testing. Our method's high sensitivity, non-destructive nature, rapid testing capabilities, and versatility make it an ideal choice for pharmaceutical manufacturers. By adhering to USP 1207, we ensure product quality, patient safety, and regulatory compliance.
In the dynamic landscape of pharmaceutical manufacturing, ensuring the integrity of packaging is paramount. USP 1207 provides a comprehensive framework for CCIT, safeguarding product quality and patient safety. At Oxipack, we are committed to aligning with these guidelines through our advanced vacuum decay method, supporting manufacturers in delivering safe and effective pharmaceutical products.