Introduction to Leak Detection in Lean Six Sigma
Lean Six Sigma, where every process improvement and efficiency gain is crucial, the integration of advanced leak detection systems plays a pivotal role. Particularly in packaging operations, where the detection of leaks can significantly streamline production and enhance quality control measures, in-line leak detection is proving indispensable.
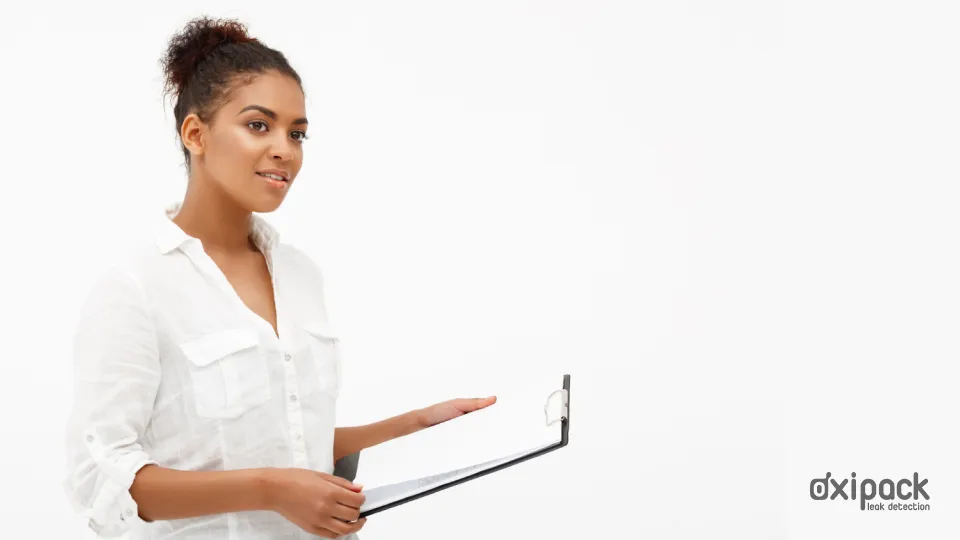
Traditional Challenges with Manual Leak Testing
Traditionally, leak detection has involved manual, random sample testing, which is especially challenging with vacuum-packed items that require hours or days before testing can even begin. Discovering leaks late in the production process not only disrupts operations but also necessitates extensive checks and potential repackaging—adding considerable time, cost, and frustration to the production cycle.
The Case for Preventative Leak Detection
Prevention is always more effective than cure, particularly in high-speed packaging environments where machine stoppages to change materials or due to leaks lead to significant operational inefficiencies. Oxipack’s automatic leak detection technology ensures that any leaks are identified during the start-up phase, thus minimizing disruptions and the potential for larger issues down the line.
Calculating ROI on Leak Detection Technology
Investing in standalone or in-line leak detection technology from Oxipack is not only a measure to improve quality but also a financially sound decision. The return on investment (ROI) can be quickly realized when considering the costs associated with:
- Lost production time due to leak checks and repackaging.
- Disposal of spoiled products and packaging.
- Potential damage to brand reputation due to consumer complaints about product quality.
Detailed Savings Analysis
Leak detection technology can result in substantial savings across the production chain by:
- Reducing the manual labor needed for leak checks.
- Decreasing the frequency of product recalls and customer complaints.
- Minimizing waste from spoiled goods.
- Eliminating the need for extensive storage space during delayed testing periods.
In the food products sector alone, savings of one to two tonnes in euros per packaging line per year are achievable, depending on the specific circumstances and product types.
Enhancing Process Control with Automatic Leak Detection
Oxipack’s in-line leak detection systems allow operators to immediately detect and address leaks, testing either all packages or a predetermined percentage. This immediate feedback loop ensures that even the smallest leaks, which might traditionally go unnoticed for up to 24 hours, are promptly identified and corrected. This proactive approach not only supports Lean Six Sigma initiatives but also moves operations towards achieving 100% output efficiency.
Achieving 100% Output with In-line Leak Detection
Implementing in-line leak detection is more than a quality control measure—it's a strategic enhancement to the manufacturing process. By enabling more effective monitoring and control, Oxipack’s solutions ensure that the packaging process suffers minimal disruptions and maintains a consistently high level of productivity. Ultimately, this leads to a scenario where no leaks are detected, and the packaging line operates at peak efficiency, embodying the Lean Six Sigma goal of perfection in production processes.
Want to learn more about integrating Oxipack’s leak detection systems into your production line? Contact us today to see how we can help you achieve operational excellence and improve your bottom line.