Spray bottles are a common packaging solution across various industries, including cosmetics, cleaning products, and pharmaceuticals. Effective leak detection is crucial to ensure that the contents are delivered in the intended manner and to maintain the quality and safety of the product. Spray bottle packaging must be rigorously tested to prevent leakage that can lead to contamination, product loss, and safety hazards.
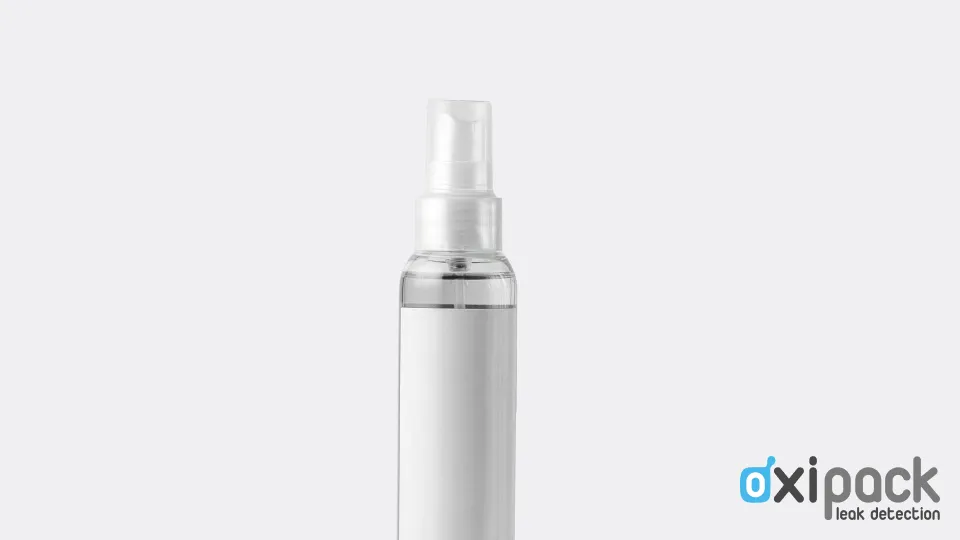
Why is Leak Detection for Spray Bottles Important?
- Consumer Safety: Leaks can compromise the sterility and effectiveness of the product, posing risks to users.
- Regulatory Adherence: Manufacturers must comply with industry standards that mandate stringent quality checks, including leak detection.
- Quality Assurance: Ensuring that spray bottles are leak-free is vital for maintaining the integrity and performance of the product.
- Cost Efficiency: Effective leak detection helps in reducing the need for recalls and wastage, directly impacting the bottom line.
- Brand Trust: A commitment to quality enhances consumer confidence and brand reputation, which are crucial for customer loyalty.
Advantages of Non-Destructive Testing in Leak Detection
Non-destructive testing (NDT) methods are particularly beneficial for checking spray bottles:
- Conservation of Products: NDT methods test the integrity of spray bottles without damaging them, allowing products that pass the test to be sold.
- Cost-Effectiveness: By not destroying the tested bottles, manufacturers save on production costs and minimize waste.
- Rapid and Accurate Results: Techniques like vacuum decay provide quick and reliable results, ensuring that production lines operate efficiently.
- Compliance with Regulations: NDT methods like vacuum decay are recognized globally and meet the compliance requirements of various regulatory bodies.
Oxipack’s Leak Detection Technologies for Spray Bottles
Oxipack offers cutting-edge leak detection systems tailored to meet the unique requirements of spray bottle packaging:
- Tailored Leak Detection Solutions: Our technology can be adapted for a range of spray bottle sizes and types, ensuring precise and effective testing.
- Automated Leak Detection Systems: Integrate seamlessly into production lines, providing continuous quality control without disrupting manufacturing processes.
- Flexible Testing Options: Whether you need to test a small batch or implement high-volume inspection, our systems provide scalable solutions.
Leak detection is a critical step in the production of spray bottles, ensuring product effectiveness and consumer safety. With Oxipack's advanced, non-destructive leak detection systems, manufacturers can achieve the highest standards of quality while optimizing production efficiency. Reach out to us today to find out how our technologies can enhance the integrity of your spray bottle products.