Ensuring Sterile Packaging Integrity in Healthcare
Imagine the potential consequences if a sterile medical device or pharmaceutical product were to become contaminated due to compromised packaging. The risks to patient safety and the integrity of healthcare products are immense. This is why sterile packaging testing is a critical process in the healthcare industry, ensuring that products remain uncontaminated and safe for use.
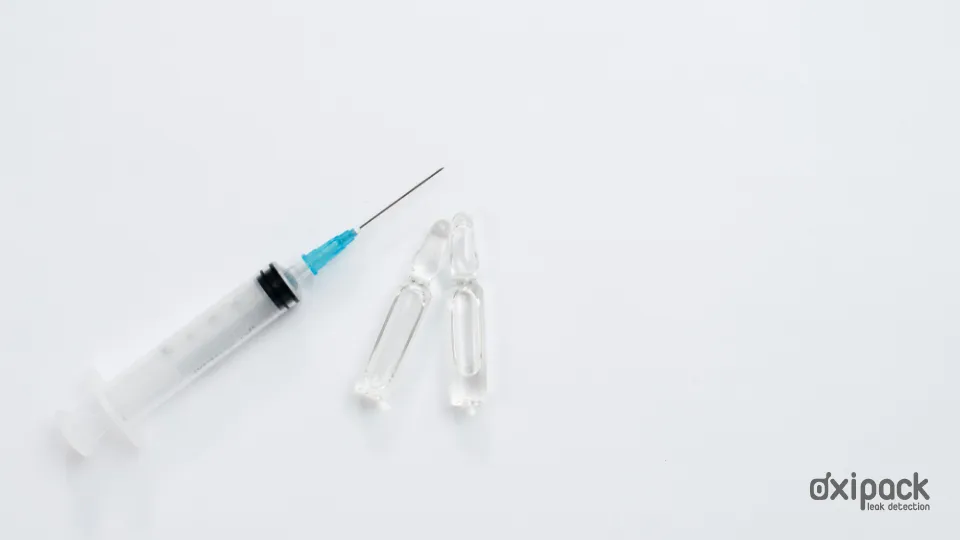
The Purpose of Sterile Packaging Testing
Sterility is a non-negotiable requirement for medical devices and pharmaceutical products. Compromises in sterility can pose significant risks to patient safety and health. Sterile packaging testing serves several vital purposes:
- Patient Safety Assurance: Sterile packaging testing ensures that medical devices and pharmaceutical products are free from microorganisms that could cause infections or health complications, especially during surgical procedures or invasive treatments.
- Quality Assurance: It is a part of the quality assurance process, confirming that packaging materials and systems are effective in maintaining sterility, preventing contamination, and preserving product efficacy and safety.
- Regulatory Compliance: Regulatory bodies like the FDA and the EMA enforce strict guidelines for sterile packaging. Sterility testing ensures compliance, allowing manufacturers to obtain necessary approvals and certifications for their products.
- Shelf-Life Determination: Through rigorous testing, manufacturers can assess the shelf life of their products, ensuring they remain suitable for use over time.
- Supply Chain Integrity: Packaging must maintain its integrity throughout the supply chain. Sterile packaging testing identifies potential weaknesses that could compromise sterility during transportation, storage, and handling.
- Product Liability Mitigation: Proper sterile testing provides evidence that manufacturers have taken necessary precautions to ensure product sterility, which can be crucial in case of legal disputes or product-related issues.
Non-Porous Sterile Barrier Testing
Sterile barrier testing is crucial for evaluating the barrier properties of packaging materials like pouches or trays. This testing ensures that the packaging system prevents microorganisms and contaminants from compromising product sterility. Non-porous packaging, which is impermeable to air, moisture, or other substances, is particularly vital for maintaining sterility.
Integrity Testers for Sterility
Several methods are used for testing the integrity of non-porous sterile packaging:
- Bubble Leak Test and Blue Dye Test: These are destructive methods that can lead to unnecessary waste and added costs. They are less preferred due to their destructive nature.
- Vacuum Decay Method: At Oxipack, we utilize the vacuum decay method, a non-destructive leak detection technique. This method is precise and ensures the integrity of medical packaging without causing any damage. Our Stationary Leak Tester (SLT), designed for flexible pouches, and the Stationary Leak Tester XS or M, suitable for healthcare tray packaging, are exemplary solutions for sterile packaging testing.
Ensuring the sterility of medical devices and pharmaceutical products is paramount for patient safety and product efficacy. Through rigorous sterile packaging testing, manufacturers can maintain high standards of quality, comply with regulatory requirements, and safeguard their products throughout their shelf life and supply chain. At Oxipack, we provide advanced, non-destructive leak detection solutions like the vacuum decay method, ensuring your products remain safe and sterile from production to patient use.
For more information on how our leak detection solutions can benefit your packaging process, please contact us.