Imagine a world where you could guarantee the safety and quality of your products without the need to sacrifice packaging or content. This is not a distant reality but a tangible possibility with the innovative Vacuum Decay Leak Test method. This cutting-edge, non-destructive testing approach ensures the integrity of packages, providing a pledge of reliability for various industries across the globe. But what makes this method so revolutionary, and how can it transform your production line? Let's dive in and discover the unparalleled advantages of vacuum decay testing.
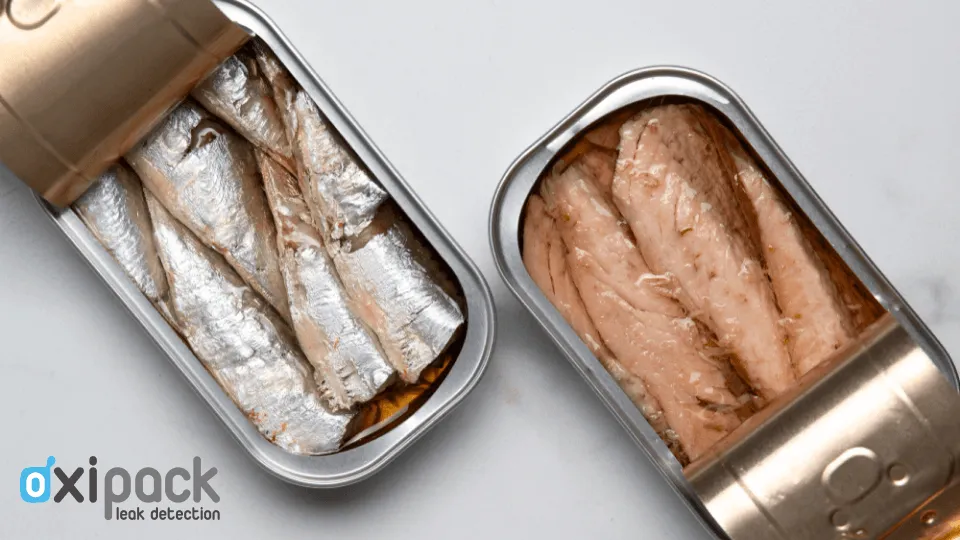
The Vacuum Decay Leak Test method emerges as a practical, highly sensitive solution for leak detection, offering dependable and precise quantitative outcomes. Employing a straightforward pass or fail assessment, numerous sectors have come to depend on it as a gold standard for integrity examination. This method is applicable for both flexible and rigid packaging, marking a significant advancement in package integrity testing.
As industries strive for excellence, the shift towards non-destructive leak testing methods to bolster quality control is clear. Identifying leaks is critical for ensuring product uniformity and excellence, especially in pharmaceutical packaging and food items. Beyond spotting package faults and unseen leakages, leak detection serves as both a qualitative and quantitative analysis tool.
The Vacuum Decay Leak Test method, endorsed as an ASTM F2338 Standard Test Method, offers a non-destructive means of identifying leaks in packaging, benefiting from technological advancements. It assesses integrity based on physical characteristics, proving to be a versatile and efficient tool.
Advantages of Vacuum Decay Testing:
This method is critical for packaging validation and quality control in various manufacturing processes. Oxipack utilizes the Vacuum Decay Leak Test to evaluate the integrity of diverse packaging forms, bringing numerous benefits:
- Non-Destructive Testing: It spares the packaging and product from damage, allowing its use across multiple production phases.
- Speed and Efficiency: Leak detection is fast, permitting the execution of numerous tests concurrently. It is also extremely easy to use.
- Sensitivity: Capable of detecting micro leaks, it stands as a highly sensitive detection method.
- Versatility: Suitable for a broad spectrum of packaging materials, sizes, and types, it's also being adopted for evaluating sustainable packaging solutions.
- Cost Savings: By identifying leaks early, it reduces product waste and rework expenses. Our white paper delves into the potential savings. (Link whitepaper her)
How It Works:
The method involves enclosing a sample within a vacuum chamber. A stable vacuum level allows for air transfer measurement from inside the package, indicating leaks through vacuum level disturbances. Oxipack's specialized membrane prevents internal pressure increase or seal stress, balancing the expanding force from the package for equilibrium, also creating a very small space surrounding the package. This facilitates the detection of both fine and coarse leaks quickly, enhancing testing throughput.
Applications Across Industries:
Vacuum decay testing has wide-ranging applications, from the food industry, ensuring packaging reliability against rancidity and contamination, to pharmaceutical packaging, where package quality is vital for maintaining drug efficacy. It's also crucial in cosmetics packaging, where product integrity directly impacts usability and consumer appeal. Additionally, this method finds use in technology sectors for component packaging integrity, safeguarding against environmental damage.
For further insights into vacuum decay leak testing or other queries, reach out to us.