In a significant move towards global standardization, a major manufacturer of specialty pet food has now installed Oxipack leak detection equipment in its 10th factory. This achievement, realized just 14 months after the first trial runs, marks a milestone in ensuring consistent quality control across all its facilities.
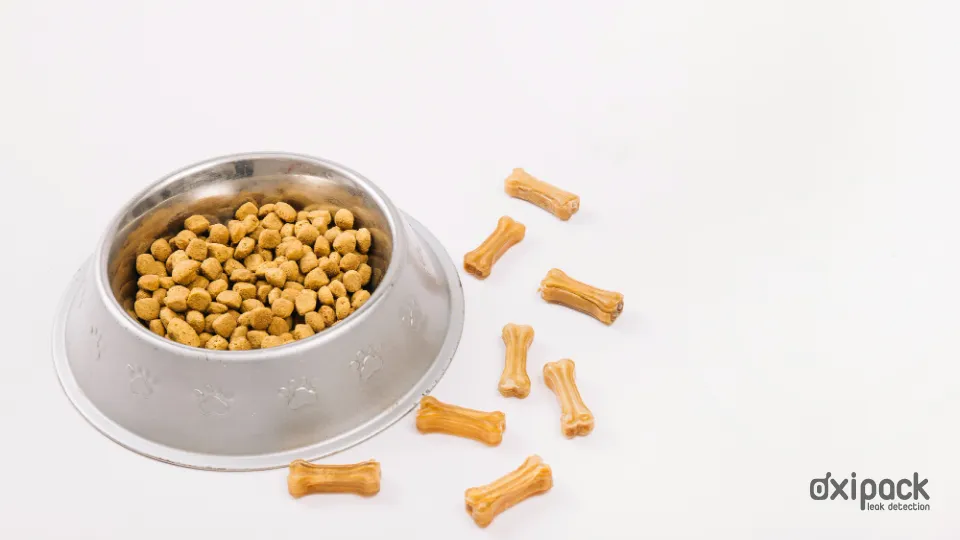
Achieving Global Standardization in Leak Detection
The journey began when the animal nutrition specialist sought a non-destructive leak detection method to replace the bubble test method traditionally used. The bubble test, which involved immersing packages in water, led to the destruction of the packaging and its contents, resulting in significant waste.
Oxipack provided the solution with its advanced leak detection technology, capable of testing the entire range of packaging without causing damage. Serge Smit, General Director of Oxipack, recalls, “The project manager invited us for a pilot trial at one of their European plants. He knew our equipment's accuracy but wanted to ensure it could match the bubble test's performance.” The trial run, which lasted one month, proved successful. The equipment demonstrated its capability to test both small 50-gram cat food containers and large 15-20 kg bags of dry dog food.
From Trial to Global Implementation
The successful trial led to an initial order for three European factories, where further tests were conducted. The results were aligned with previous methods, and adjustments were made to meet headquarters' requirements. The Oxipack Leak Tester XXXL was also refined for ease of operation. By 2015, the company began a global roll-out, extending to Africa, East Asia, North America, and Northern Europe. The most recent addition is a new plant in Asia, marking the 10th location to adopt Oxipack's leak detection technology. Concurrently, the water immersion tanks are being phased out, improving production hygiene.
Cost Savings and Return on Investment
The switch to Oxipack’s non-destructive leak detection method significantly reduces costs and prevents waste. Previously, packaging tested in immersion tanks had to be discarded. With the Oxipack Leak Tester, approved packaging can be returned to the production line, undamaged. Early adopters of the technology have reported substantial savings, with a return on investment within 6-9 months, depending on the cost of the packages tested. This rapid ROI underscores the financial and operational benefits of adopting Oxipack's technology.
Preferred Equipment for Leak Detection
Most production facilities have implemented two versions of the Oxipack Leak Tester:
- Standard Leak Tester (SLT): Suitable for small flexible packaging ranging from 2 oz to 9 lb.
- SLT XXXL: Designed for large flexible packaging, approximately 9 lb to 2 quarters, ensuring airtightness.
The collaboration between Oxipack and the global pet food manufacturer highlights a significant advancement in leak detection technology. By standardizing this non-destructive method across all its factories, the manufacturer not only ensures the integrity of its packaging but also achieves substantial cost savings and reduces waste. The global roll-out of Oxipack's leak detection equipment sets a new benchmark for quality control in the pet food industry, ensuring consistent, high-quality products worldwide.