As marketeers and packaging designers continually innovate, they introduce revolutionary packaging solutions that demand equally advanced testing technologies. A prime example is the Senseo Sarista, a system that uniquely feeds fresh coffee beans from individual plastic containers into a coffee machine, ensuring the coffee remains fresh.
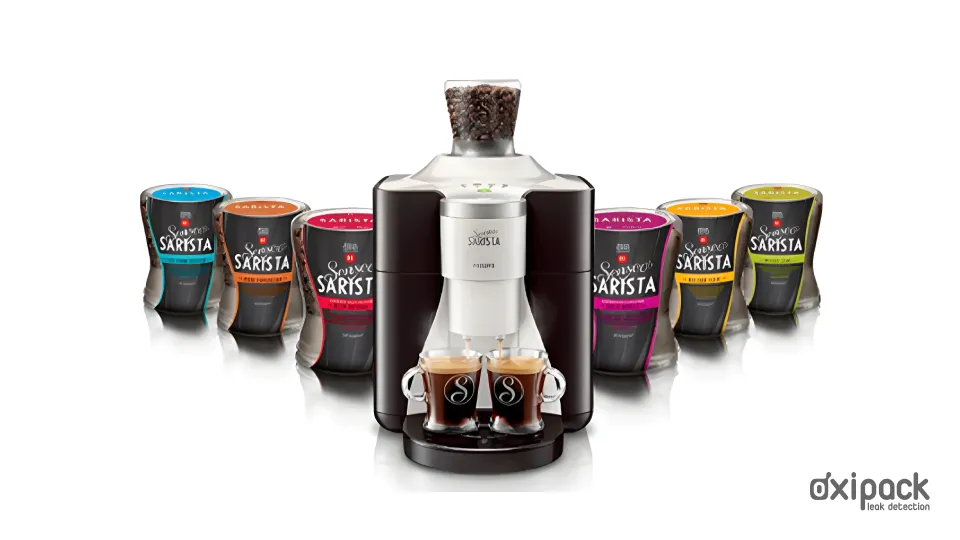
Recognizing the critical importance of maintaining freshness, Douwe Egberts Master Blenders sought a reliable method to test the integrity of this new packaging. Given that the existing equipment was inadequate for the Sarista's unique design, Oxipack was called upon as the preferred partner to develop a non-destructive leak detection solution tailored specifically for this challenge.
Customized Leak Detection Process
The solution involved a specially developed tester—dubbed the Senseo Sarista Tester—that utilizes a flexible rubber cowl to conform precisely to the packaging's unique contours. Here’s how it works:
- Initial Setup: The rubber is housed within a bell jar and initially expanded outward, allowing the jar to easily encompass the packaging.
- Vacuum Application: Once positioned, the rubber cowl is released, snugly fitting around the packaging. The surrounding air is then evacuated, creating a vacuum, which facilitates an accurate measurement of air pressure within seconds.
- Rapid Testing: The entire test is quick, taking about thirty seconds, and is simple enough to be operated directly by production staff. A change in air pressure between measurements signals a leak, triggering a red light to alert the operator for immediate action.
Adaptability for Various Packaging Types
This innovative setup is not just limited to Senseo Sarista but can also be adapted for various types of rigid packaging. Oxipack specializes in custom-developed, non-destructive leak detection equipment that measures minute pressure differences, making it a unique global provider.
Integrating Leak Detection Early in Design
Incorporating leak detection early in the design process is crucial. It’s easier to adjust design details during the initial stages than after production has begun. Engaging with packaging technologists, engineers, or R&D departments early on ensures that all necessary leak detection features are considered:
- Necessity of Leak-Free Packaging: Determining if the product must be completely leak-free.
- Testing Capabilities: Assessing whether the packaging can be tested for leaks and if in-line, non-destructive testing is feasible.
- Compliance and Equipment Needs: Ensuring the design complies with required standards and assessing if existing equipment suffices or if new solutions are needed.
Prototype Testing and Custom Solutions
For new packaging concepts, Oxipack provides options to test prototypes or initial production runs using standalone equipment. This helps establish a quality benchmark early on. For packaging designs that are challenging to test with current methods, Oxipack’s expertise in crafting customized solutions comes into play, offering new avenues for addressing complex leak detection challenges.
Are you ready to ensure your innovative packaging is leak-free with Oxipack’s cutting-edge solutions? Contact us to explore how our tailored technologies can enhance your product’s integrity.