A few years ago, a UK-based injection moulder specializing in medical devices for treating diabetes and lung diseases approached Oxipack with a unique challenge. They needed to ensure that their transport packaging for medical device components was airtight to prevent contamination by ambient air. The packaging, a large aluminium foil pack roughly 18 x 22 x 25 inches in size, was atypical due to its cube shape and flexible structure, described technically as a quadruple stand-up pouch.
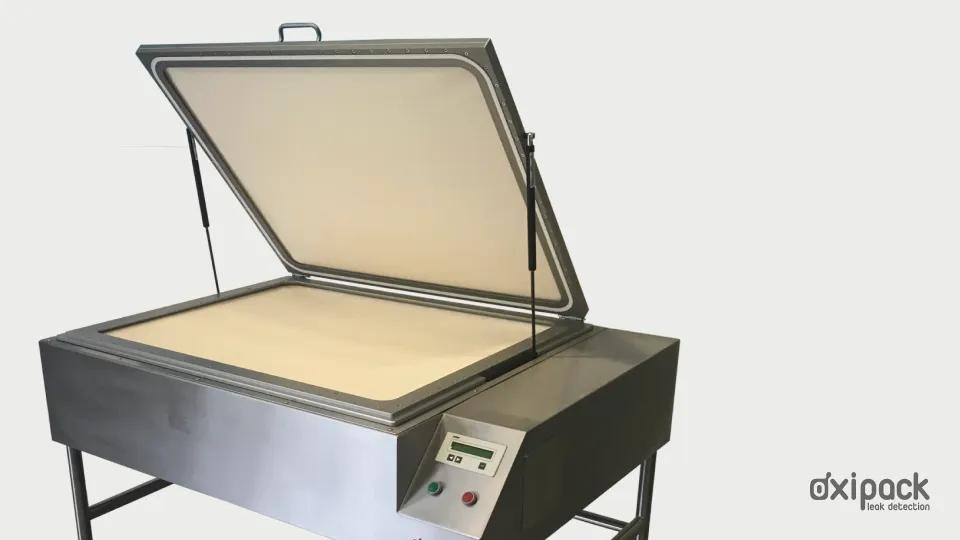
Custom Leak Detection Solution
Recognizing the critical nature of the request, Oxipack’s team engaged in a rigorous analysis and discussion. The conventional bubble leak test method was unsuitable due to the packaging's large dimensions and the presence of folds that could trap air bubbles. The challenge was clear: develop a non-destructive method capable of testing these large, cubical packages for airtightness with precision down to 50 microns.
Prototype Development and Testing
In response, Oxipack designed a prototype featuring a custom-made rectangular bell jar tailored to the package's dimensions. This innovative approach allowed for accurate detection of even minuscule leaks, showcasing Oxipack’s ability to reach a new level of precision in leak detection—potentially down to 25 microns. Testing of the initial packages revealed that three of the four sent were not airtight, confirming the need for a robust leak testing process at the production stage.
Oxipack Leak Tester XXXL
Driven by the successful prototype, Oxipack developed the Leak Tester XXXL for mass production use. This giant tester, nearly 8 feet tall and weighing 400 kg, was designed to handle the packaging sizes with the same high accuracy, regardless of the contents’ physical characteristics. Notably, this machine included an extra built-in security feature to meet the stringent quality standards required in the medical industry, ensuring that any detected leaks were genuinely from the packaging and not from the testing equipment itself.
Successful Implementation and Future Prospects
The completion of the Leak Tester XXXL marked a significant milestone for Oxipack. Two units were crafted and shipped to the client’s factory in England, where Oxipack technicians conducted on-site installation and training. The operations manager expressed satisfaction with the system, particularly appreciating how the new sealers could be validated simultaneously.
Reflections and Future Challenges
Reflecting on this project, Serge Smit, a lead at Oxipack, commented, "By developing this specific leak tester, we proved that we can handle all types of challenges. So I dare say: Bring it on, challenge us! With our knowledge and expertise, we are ready to find solutions to meet the client’s needs."
As to how large Oxipack can test? “Try us. We can test really big bags,” says Serge. And regarding the future, he hints, “It might get even bigger. We might even test entire shipping containers for air-tightness using a different process. But whether it is necessary? Time will tell.”